Cleaner Air Oregon is a health-based permitting program that regulates emissions of toxic air contaminants from facilities based on risk to nearby communities. CAO requires facilities to report toxic air contaminant emissions, assess potential health risks to people nearby and reduce toxic air contaminant risk if it exceeds legal limits.
As part of the Cleaner Air Oregon process, each facility has a dedicated web page to provide communities access to facility information and updates on where it is involved in the process.
- Each step of the CAO risk assessment process has a section that includes DEQ's communications and deliverables from the facility.
- The graphic below shows where a facility is in the Cleaner Air Oregon Process.
For additional information and history of the program, visit the Cleaner Air Oregon web page.
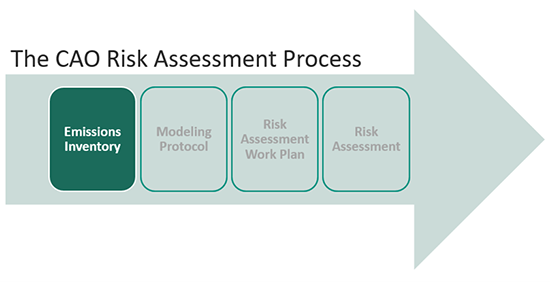
The Emissions Inventory provides information on all the Toxic Air Contaminant emissions from a facility, and includes information on a facility’s operations and activities, as well as fuel and material usage rates. This is often the longest step in the CAO risk assessment process as DEQ needs to verify that all activities have been accounted for, and that the most representative emissions data available are used. In some cases, DEQ will require a facility to perform source testing at this stage if insufficient data is available to estimate emissions.
March 1, 2022: Facility called in to CAO program.
May 31, 2022: Facility submitted Emissions Inventory and supporting information (currently in DEQ review)
Feb. 6, 2024: DEQ responds to the Emissions Inventory submittal with a request for revisions and additional information.
April 22, 2024: Facility submitted Emissions Inventory extension request.
April 24, 2024: DEQ responded to Emissions Inventory extension request.
April 24, 2024: DEQ requests additional information.
May 6, 2024: Facility submitted additional information regarding the Emissions Inventory (in DEQ review)
About the Facility
Georgia-Pacific Toledo LLC produces pulp and paper products from a variety of virgin wood chips and recycled fibers. Pulp is produced using Kraft (sulfate), modified Kraft (semi-chemical), and recycling processes. Other major processes at the facility include material handling, steam and energy production, chemical recovery and byproducts, paper production, and product handling and shipping. The mill is located within the city limits of Toledo and has been operating since 1957.